A centrifuge is a device used to spin small liquid samples at high speed in order to separate parts of the liquid (or mixture really) based on their density. They are used for all sorts of applications where you might want to separate solids from liquids in a mixture, one example is separating different components in a blood sample so each can be tested.
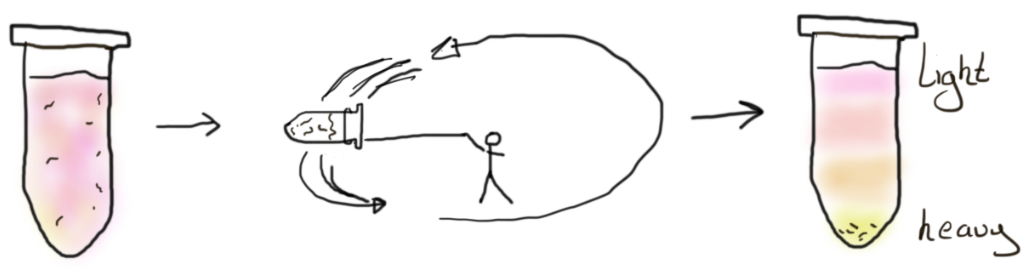
This work was done for the Adaptive & Responsive Nanomaterials Group at UCL. They required a centrifuge that could operate autonomously within an existing pipetting robot. They could not find an off the shelf device that met their requirements:
- Small size (50x50x50 cm), in order to fit into the device.
- Have positional control, so the location of samples would be known by the robot.
- Be designed such that the pipetting robot could add and extract samples.
These requirements throw up a few issues, first the centrifuge motor (or motors) would have to spin the rotor at very high speed and very low speed. Second, in order to play nice with the robot pipette the rotor itself would have to be a ‘swinging bucket’ type. This design allows the sample to sit upright when stationary (easy access for the pipette) and horizontal when being spun. A fixed angle design wouldn’t have allowed the pipette to reach the bottom of the sample container.
I started with an off the shelf ‘mini centrifuge’ to get me started and began pulling it apart, the first prototype looked like this:
I could not find a motor that could accurately position at low speed and also spin at the very high rpm required (A stepper motor is probably the closest option) so the first idea was to have two motors, one for each task. The downside to this is increased complexity as the motors need to be able to engage and disengage somehow. I stumbled upon a simpler option. If you send a single pulse of current through the coils of a DC motor you can gently nudge it through the natural positions of the rotor (governed by the magnets and coils in the motor). This gives you a crude but effective way of positioning the rotor. This coupled with an optical position sensor enabled the system to find a ‘home’ position. The position of each sample when at this home position could then be programmed into the pipetting robot.
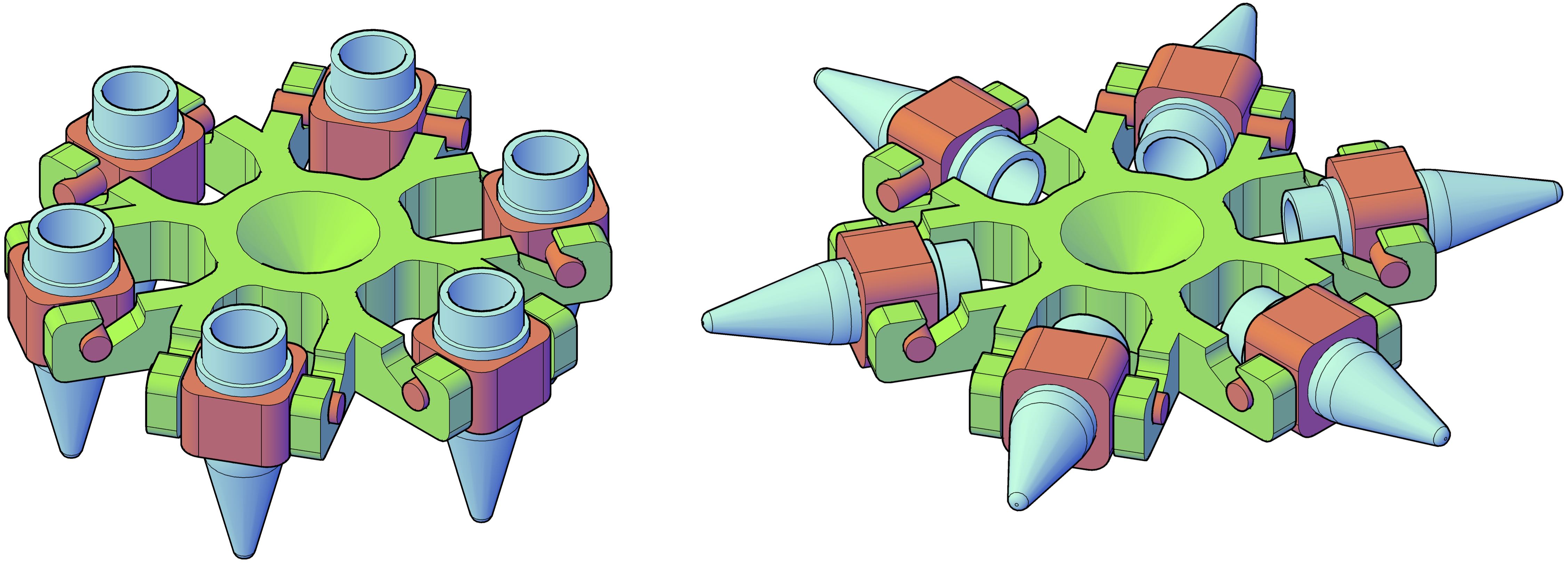
The second challenge was the swinging bucket rotor / sample holder. These are usually seen on very large centrifuges, not small ones. So I designed a scaled down version and 3-D printed a prototype, this worked great and so an aluminium version was experty cnc-ed at the Chemical Engineering dept. Workshop.
The final device looked like this. A fancy aluminium case and protective shroud was added. An arduino controls everything and the code contains a few fail-safe measures in-case the home position cannot be reached.
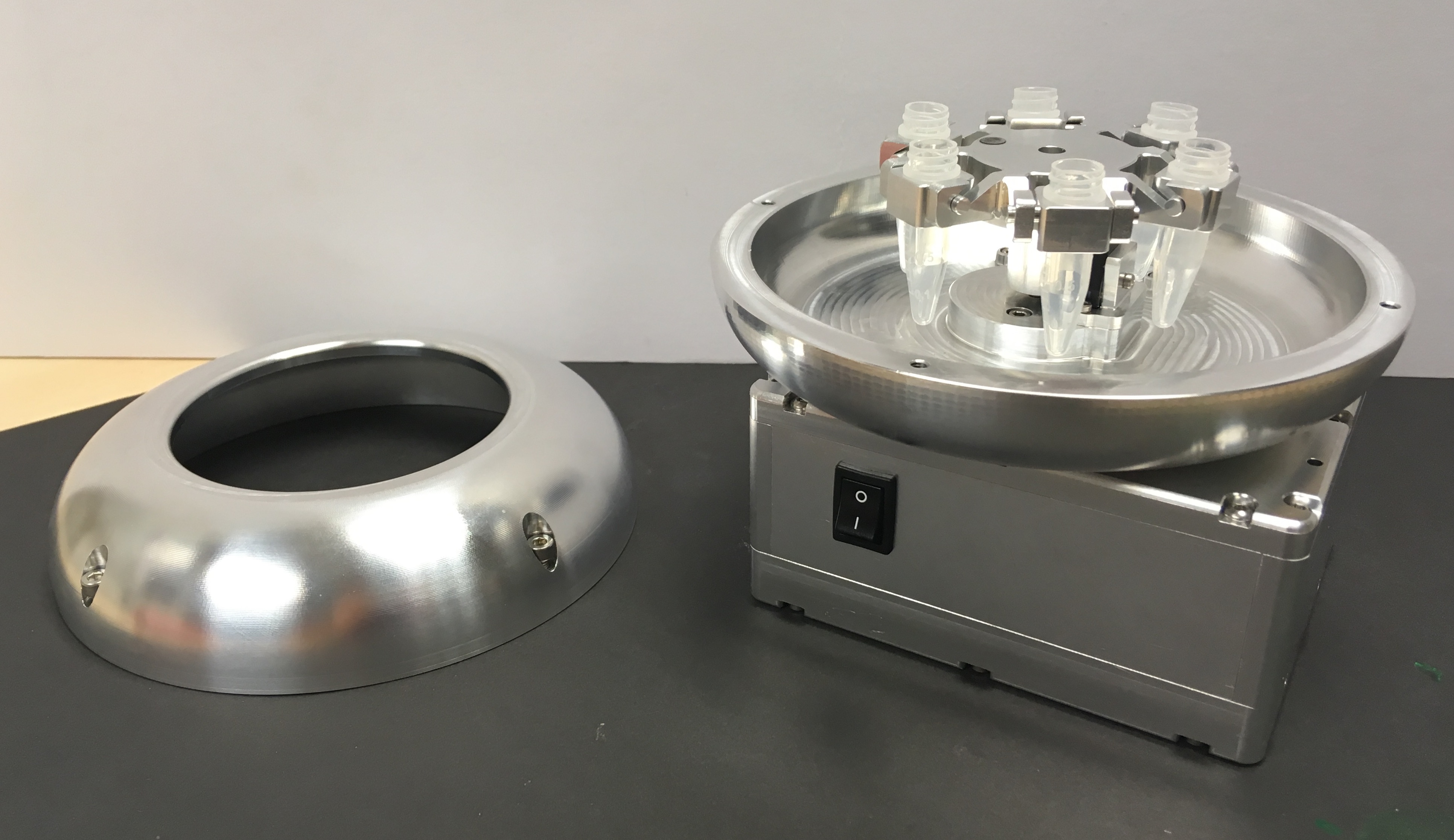